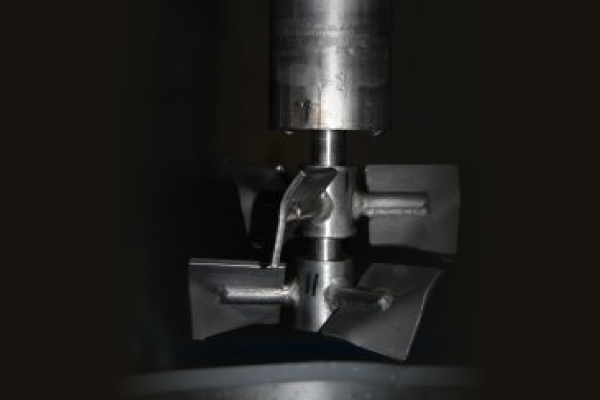
Projektowanie procesów mieszania
Procesy mieszania mają ogromne znaczenie w praktycznie każdej gałęzi przemysłu, ponieważ odpowiednie wymieszanie substancji ma często decydujący wpływ na jakość wytwarzanego produktu. Metody projektowania takich procesów wciąż są udoskonalane i w coraz większym stopniu oparte na obliczeniach numerycznych. W tym wpisie przedstawimy nasze Pro-millowe podejście do zagadnienia, oparte na najnowszej wiedzy i nowoczesnych narzędziach, takich jak mieszalniki czy homogenizatory.
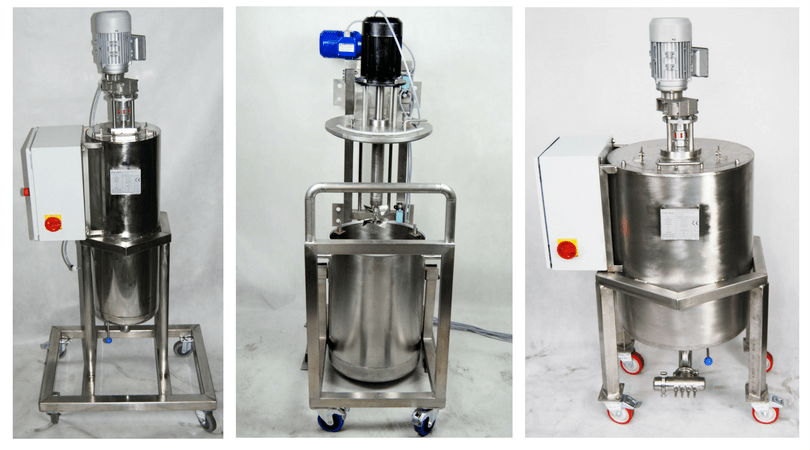
Od czego zacząć projektowanie procesu mieszania?
– Procedurę projektowania procesu mieszania należy rozpocząć od analizy właściwości surowców, które mają zostać wymieszane. Istotne jest także, jaki jest cel mieszania: jaki układ chcemy uzyskać i jaki stopień wymieszania będzie zadowalający. – mówi inż. Karol Strzyż, główny technolog procesowy firmy Pro-mill.
W zależności od tego, czy mamy do czynienia z układem ciecz-gaz, ciecz-ciecz czy ciecz-ciało stałe stosuje się różne metody mieszania. Wzajemne oddziaływania między substancjami, a także ich właściwości również należy wziąć pod uwagę. W przypadku gazów musimy uwzględnić wielkość pęcherzyków, w przypadku cieczy – jej gęstość i lepkość. W przypadku ciał stałych – zakres wielkości cząstek i ich gęstość. Na tej podstawie podejmujemy decyzję o rodzaju mieszania – czy mieszanie ma być osiowe, promieniowe, itd. A jak już to ustalimy kolejnym krokiem jest dobór mieszadła i policzenie wymaganej mocy mieszania.
Pierwszy krok – obliczenia procesowe dotyczące mieszania
W projektowaniu procesów mieszania bardzo pomocne są specjalistyczne programy komputerowe, jak np. Solid Works Flow Simulation. Symulacje pozwalają na badanie ruchu cieczy w zadanych warunkach oraz analizę sił działających na komponenty zanurzone w cieczy. Dzięki temu możliwe jest przetestowanie różnych rozwiązań, a w efekcie dobór tego najbardziej odpowiedniego.
Bardzo często mamy do wyboru kilka różnych konstrukcji mieszadeł, których skuteczność można weryfikować za pomocą już wspomnianych symulacji komputerowych. Zaprojektowane mieszadło, poza umożliwieniem uzyskania wymaganej efektywności mieszania, powinno być jak najprostsze do wykonania i jak najmniej awaryjne. Często wystarczy zastosować zwykłe mieszadło łopatkowe, które ma stosunkowo prostą konstrukcję. Geometrię łopatek, ich rozmieszczenie, nachylenie, krzywiznę, itd. można dobrać wykonując symulacje i analizując wywołany przez nie przepływ. Daje to nam również informację o dostępnej mocy mieszania, a co za tym idzie o odpowiedniej prędkości obrotowej wału mieszadła. Dobrym punktem wyjścia do takich rozważań są poprzednie projekty, wykazujące podobieństwo do obecnie wykonywanego, oraz analiza wymiarowa. Można z nich zaczerpnąć wstępny zakres częstości obrotowej, w którym z dużym prawdopodobieństwem zawiera się odpowiednia dla nas wartość. Doświadczenie i wyczucie projektanta są więc nieocenione i znacznie skracają czas pracy nad projektem.
Aspekty konstrukcyjne i „iteracje”
To co z procesowego punktu widzenia wydaje się najlepszym rozwiązaniem, nie zawsze jest możliwe do osiągnięcia, a czasem wręcz niewykonalne, biorąc pod uwagę samą mechanikę konstrukcji. Dlatego w trakcie projektowania istotna jest ścisła współpraca inżyniera procesowego z inżynierem mechanikiem. Pozwala to uniknąć błędów i opóźnień już na etapie produkcji urządzenia.
Praca inżyniera mechanika rozpoczyna się w momencie, kiedy znana jest już najbardziej odpowiednia z punktu widzenia procesowego geometria mieszadła oraz wymagana moc mieszania. Wtedy, wychodząc z mocy mieszania, oblicza się potrzebny moment obrotowy na wale mieszadła, a następnie dobiera się odpowiednią przekładnię i silnik. Kolejnym krokiem jest wykonanie obliczeń wytrzymałościowych, w których ponownie bardzo pomocne są symulacje, np. w programie Solid Works Simulation.
– Najważniejsza jest weryfikacja naprężeń działających na mieszadło, które są spowodowane głównie przez dwa czynniki: siłę odśrodkową i opór płynu – wyjaśnia inż. Rafał Marciniak, główny konstruktor firmy Pro-mill. – Musimy zadbać, aby granica plastyczności nie została przekroczona – nasze mieszadło nie może pod wpływem pracy ulec stałym odkształceniom.
Podczas symulacji wytrzymałościowych sprawdzamy, czy w układzie nie występują węzły, w których przekroczono dopuszczalne naprężenia. Węzły takie mogą wystąpić np. w miejscu łączenia elementów pod kątem prostym, na ostrych krawędziach itd. Zwykle bardzo łatwo można wyeliminować problem przez nawet delikatne zaokrąglenie krawędzi.
– Każdorazowo jednak należy zweryfikować nawet najmniejszą zmianę geometrii przez powtórzenie symulacji procesowych i sprawdzić, czy nadal udaje nam się osiągnąć odpowiedni stopień wymieszania – zauważa inż. Karol Strzyż.
Współpraca inżyniera procesowego z inżynierem mechanikiem jest więc procesem w pewien sposób iteracyjnym. Interdyscyplinarne podejście do zagadnienia pozwala na stworzenie projektu, który nie będzie wywoływał problemów już na etapie produkcyjnym. Warto też na bieżąco konsultować projekt z pracownikami warsztatu, np. spawaczami, którzy potem będą nasz projekt urzeczywistniać. Pozwoli to wychwycić wszelkie problemy konstrukcyjne jeszcze przed rozpoczęciem produkcji, a to znacznie redukuje ryzyko wystąpienia błędów i opóźnień.
Sterowanie
Bardzo ważną osobą, która pracuje nad projektem, poza już wcześniej wspomnianymi, jest automatyk, zajmujący się sterowaniem całym urządzeniem.
– Praca nad układem sterowania rozpoczyna się od zebrania informacji, co urządzenie ma dokładnie robić, jakie są ograniczenia konstrukcyjne, jakie jest obciążenie mocy układu, ile będzie sterowanych elementów, jak one mają działać, itd. – wyjaśnia inż. Artur Uzarski, główny automatyk firmy Pro-mill.
Automatyk projektuje cały układ sterowania, którego praca polega na zbieraniu sygnałów z poszczególnych przetworników, interpretacji i przetwarzaniu ich oraz wysyłaniu sygnałów sterujących do odpowiednich urządzeń wykonawczych. W takich układach wykorzystuje się sterowniki PLC (ang. Programmable Logic Controller), których algorytm działania musi zostać zapisany w dedykowanym dla danego sterownika języku programowania. Sterowniki PLC posiadają kolorowe, dotykowe ekrany, które umożliwiają bardzo łatwą obsługę urządzenia. Układ sterowania zabezpiecza sterowany obiekt przed uszkodzeniem, realizując zadaną procedurę bezpieczeństwa.
Podsumowanie
Proces mieszania to jedna z najważniejszych operacji jednostkowych, wykorzystywanych w przemyśle, która umożliwia skuteczne łączenie różnych substancji. Na skuteczność mieszania ma wpływ wiele parametrów. W celu znalezienia odpowiedniego rozwiązania dla danej sytuacji warto korzystać z nowoczesnych narzędzi numerycznych, które pozwalają na symulacje procesu. Istotne jest także kompleksowe podejście do zagadnienia, polegające na współpracy inżyniera procesowego, konstruktora i automatyka. Zapewnia to szybką i bezproblemową realizację projektu.