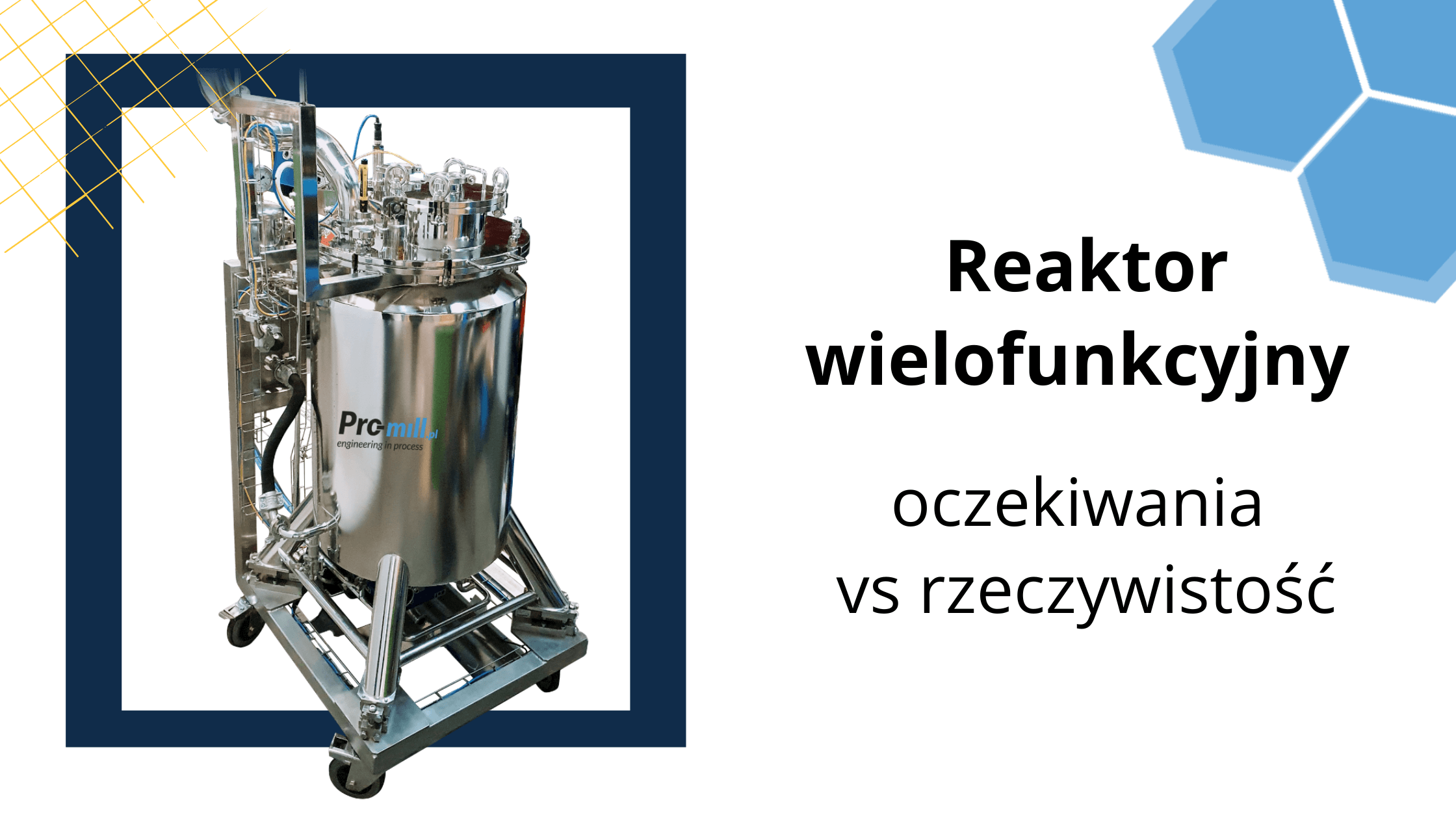
Reaktor wielofunkcyjny – oczekiwania vs rzeczywistość
Idea reaktorów wielofunkcyjnych polega na integracji różnych procesów w obrębie jednego urządzenia. Szczególnie istotne może się to okazać w przypadku skomplikowanych linii technologicznych czy w wieloetapowych recepturach wytwarzania produktu. Taki reaktor wielofunkcyjny warto wziąć pod uwagę także przy instalacjach pilotażowych, służących do zwiększania skali procesów laboratoryjnych. W efekcie tak zaprojektowanej instalacji, można wyeliminować część maszyn z ciągu technologicznego. Co potencjalnie możemy na tym zyskać? Od skrócenia czasu procesu, przez ograniczenie wymaganej powierzchni hali produkcyjnej, po oszczędności pieniędzy bezpośrednio wynikające z kupna mniejszej liczby maszyn. Brzmi zachęcająco? 🙂
Reaktory wielofunkcyjne Pro-mill
W tym roku mieliśmy okazję wykonać reaktor wielofunkcyjny, pełniący funkcję instalacji pilotażowej. Klient zgłosił się do nas z chęcią przetestowania swojego procesu w większej skali. Przez wiele lat, skrupulatnie pracując w laboratorium, opracował proces wytwarzania interesującego go produktu. Na spotkaniu podzielił się z nami swoją koncepcją.
Wspólne spotkania z Tobą traktujemy bardzo poważnie – to Ty jesteś naszą skarbnicą wiedzy o Twoim procesie. Projektując Twoją instalację bazujemy na zebranych od Ciebie informacjach, łącząc to z posiadaną przez nas wiedzą i doświadczeniem inżynieryjnym.
Wspólnie ustaliliśmy zakres projektu oraz funkcjonalności docelowej instalacji. Uścisnęliśmy sobie dłonie i rozpoczęliśmy współpracę. Wszystko wskazywało na to, że kolejny projekt zakończony będzie sukcesem. Pełni entuzjazmu zabraliśmy się do projektowania urządzenia, jakiego na rynku jeszcze nie było. Czy wszystko poszło tak, jak zakładaliśmy? Nic bardziej mylnego. To co się wydarzyło?
Problemy w skalowaniu procesów
Jak to często przy skalowaniu procesów bywa, to co sprawdza się w laboratorium, niekoniecznie sprawdza się w większej skali. Dlatego wspólnie z naszym klientem, przeprowadzaliśmy testy instalacji, aby sprawdzić, jakie rozwiązania sprawdzą się w większej skali.
Więcej na temat skalowania procesów przeczytasz TUTAJ.
Szczęśliwie na etapie projektowania zdecydowaliśmy się na reaktor wielofunkcyjny. Dzięki temu podczas testów mieliśmy szansę zintegrować różne procesy, a także wymienić niesprawdzające się moduły.
Jako, że dążymy do szczęśliwych zakończeń, modernizowaliśmy nieco nasz chemiczny reaktor wielofunkcyjny. Finalnie maszyna pozwala na prowadzenie pożądanego procesu Klienta. Dzięki temu nasz Klient może ze spokojną głową pracować nad swoim produktem w większej skali.
Jakie procesy można połączyć w reaktorze?
Przemyślany projekt urządzenia może sprawić, że nie będziesz potrzebował wielu maszyn, aby wytworzyć pożądany produkt. Mieszanie, filtracja, destylacja, ekstrakcja – to propozycja procesów, które połączyliśmy w ramach reaktora wielofunkcyjnego. Każdy z nich można prowadzić po kolei lub korzystać tylko z wybranych, aby otrzymać zupełnie nowe możliwości, np. zwiększyć wydajność procesu. Aby zrealizować pożądane procesy, trzeba wyposażyć instalację w niezbędne komponenty.
Po pierwsze – mieszanie
Zadaniem mieszania jest połączenie składników oraz intensyfikacja procesów. Coraz częściej spotyka się maszyny z możliwością zmiany położenia mieszadła na wale. Pozwala to na wybór objętości roboczej reaktora, szczególnie ważnej przy urządzeniach pilotażowych lub produkowaniu różnych produktów w jednym urządzeniu. Układ mieszania dobieramy m.in. w zależności od składników procesu.
Więcej o doborze mieszadeł przeczytasz TUTAJ.
Procesy separacji
Na system separacji składa się filtracja, destylacja i ekstrakcja. Są to metody powszechnie stosowane do rozdziału składników. Takie połączenie procesów pozwala na rozdział lotnych związków poprzez destylację, rozdział cieczy poprzez ekstrakcję, a także rozdział cząstek stałych poprzez separację mechaniczną na przegrodzie. Ale w jaki sposób zaimplementować je w reaktorze?
Po drugie – filtracja
Filtrację można zrealizować za pomocą różnego rodzaju membran lub koszy umieszczonych bezpośrednio w zbiorniku. Dobór odpowiedniej przegrody filtracyjnej pozwala na separację ciał stałych od cieczy. Natomiast za pomocą podciśnienia lub nadciśnienia, można w dowolnym momencie wymusić proces filtracji.
Po trzecie – destylacja
W celu przeprowadzenia destylacji, zbiornik wyposaża się w instalację grzewczo-chłodzącą, chłodnicę oraz niezbędną aparaturę kontrolno-pomiarową, aby móc regulować parametry procesu. Mieszanina znajdująca się w zbiorniku jest podgrzewana do osiągnięcia temperatury wrzenia jednego ze składników, a opary są skraplane na chłodnicy. Tym samym zachodzi separacja składników ciekłych.
Po czwarte – ekstrakcja
Ekstrakcja zachodzi poprzez dodanie odpowiednich składników bezpośrednio do zbiornika. Może występować w układzie ciecz-ciecz, jak i ciecz-siało stałe. Wyekstrahowane składniki można oddzielić np. na membranach lub w rozdzielaczu. Jeśli do procesu użyto ciała stałego, podczas drenażu cieczy warto zastosować układ filtracji, aby odseparować niepotrzebne cząstki.
Na co jeszcze zwrócić uwagę? Strefa wybuchowa EX
Ze względu na szerokie funkcjonalności reaktorów wielofunkcyjnych, warto przemyśleć, jakie składniki będą używane do procesów. Czy są one substancjami niebezpiecznymi lub palnymi? Jeśli tak, nie ma problemu, dostosujemy Twój reaktor do pracy w strefie zagrożonej wybuchem.
Jednym z ważniejszych etapów podczas wyboru instalacji do Twojego procesu, jest dokładna analiza pożądanego procesu. Może okazać się, że pomimo skomplikowanego procesu i początkowo dużej liczby wyspecyfikowanych maszyn, nie będzie Ci to potrzebne. Nie zawsze więcej znaczy lepiej. Warto zastanowić się nad przebiegiem procesu i zoptymalizować docelową instalację, zarówno pod kątem liczby maszyn, jak i parametrów procesu.